Businesses have witnessed many revolutions since 1760. It has come so far now that manufacturers have started combining physical production processes with digital technology, smart computing, and big data. This amalgamation of technologies is increasingly helping companies create their revenue sources from manufacturing and supply chain management.
The data revolution helps factories evolve and rethink their automation strategies and workforce. In this article, we will cover the importance, benefits, and challenges of the smart factory and help you understand how to implement it and garner more revenue.
Money, ease of use, and integrated system architecture
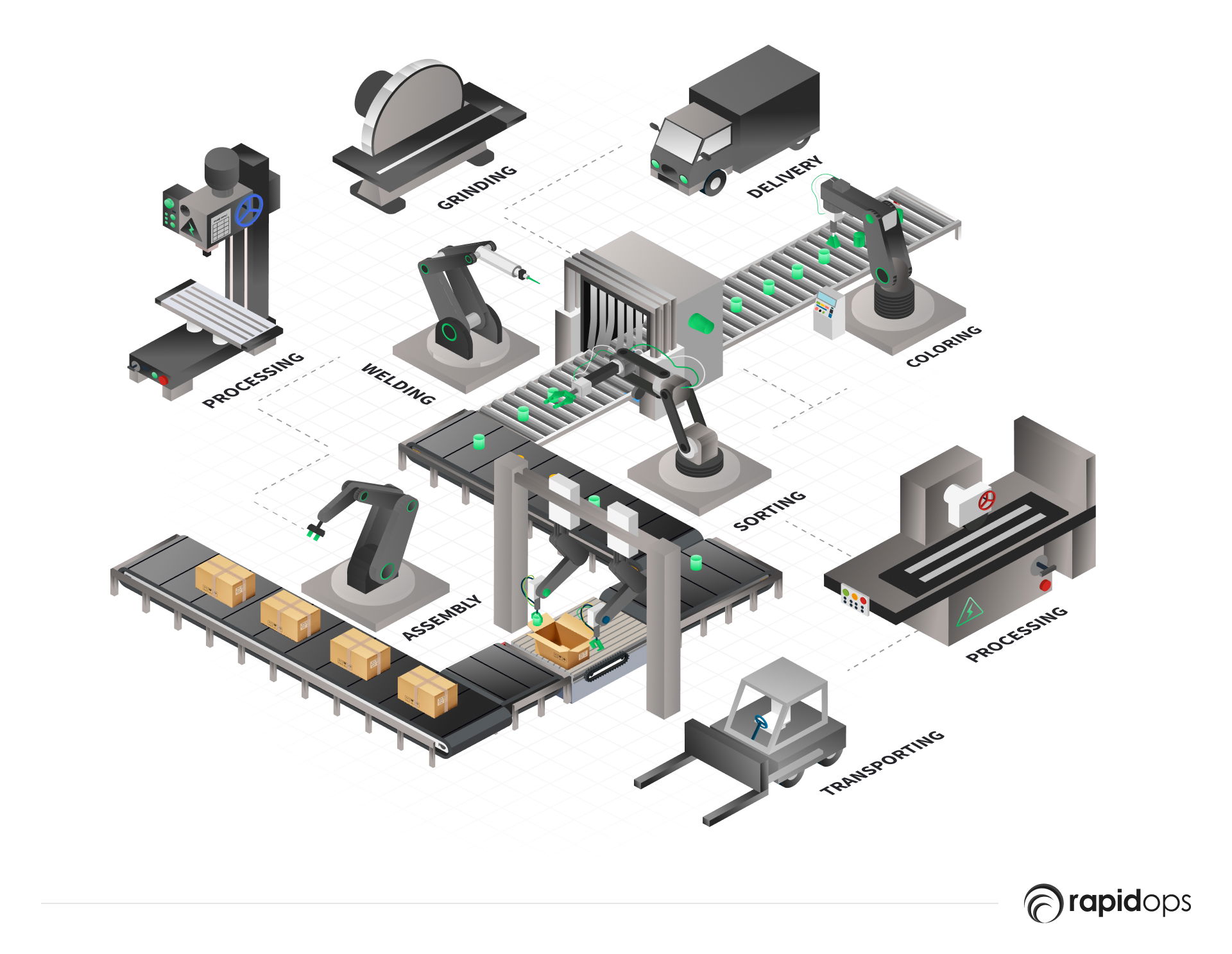
The prognosis for worldwide spending on IoT by 2023 was 1.1 trillion U.S. dollars, as estimated in 2019. Region-wise, the Asia Pacific region held the largest share of the IoT market. North America came in second, followed by Europe, Middle East and Africa. - Statista
To give you a quick overview, a smart factory is a digitized system that continuously collects and shares crucial data via connected machines, smart devices, and production units. Self-optimizing devices then utilize the collected data for:
- Discovering and countering various issues
- Improving the manufacturing processes
- Gauge various demand parameters
A smart factory is primarily used in manufacturing companies by implementing modern technologies like robotics, artificial intelligence, big data analytics, cloud computing, and industrial IoT (Internet of Things).
These technologies have made their contribution felt in mainstream smart manufacturing practices because they can run autonomously coupled with the capability to self-correct. Being an important outcome of the fourth industrial revolution, popularly termed Industry 4.0, it is the factory of the future that is still in its early days.
Once implemented, manufacturers can utilize cloud technology for storing and accessing vast data pools for operating and maintaining manufacturing applications within their factories or across their supply chains.
A brief contribution of Factory 4.0
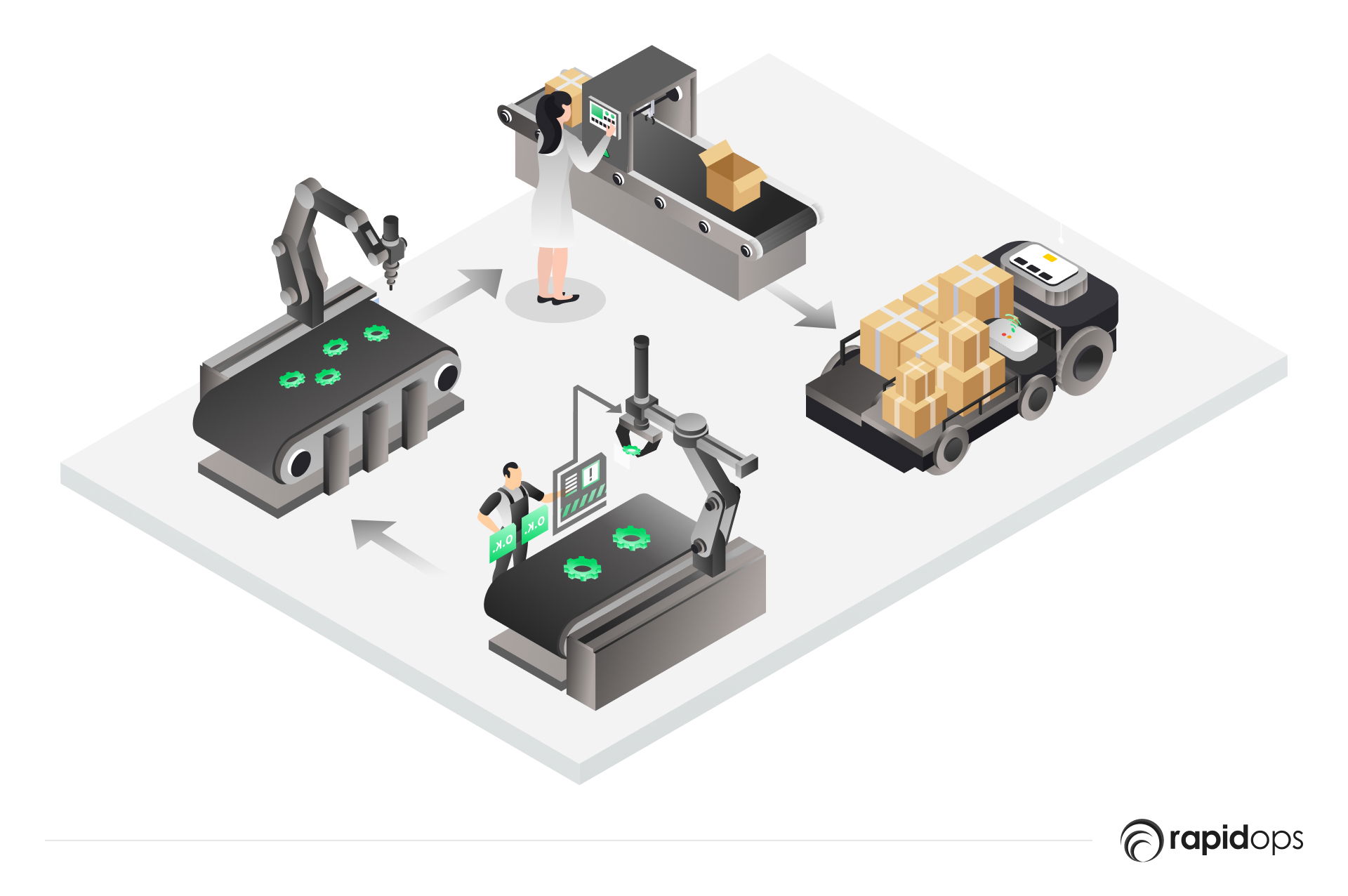
Smart factory, as explained earlier, is the result of a new phase in the industrial revolution. In this phase, factories are evolving by heavily focusing on:
- Gathering real-time data
- Embedded sensors
- Connectivity automation
- Machine learning
The structure of a smart factory includes production, information, and communication technologies. These individual structures can be integrated across the entire manufacturing supply chain. Manufacturers can integrate these disparate parts using IoT and various other advanced integrated circuits.
These circuits can enable sensing, measurement, control, and communication of connected devices involved in the manufacturing process.
A smart factory denotes a leap forward from more traditional automation to an infrastructure that comprises a completely connected and flexible system of smart devices.
These devices utilize a constant stream of data via connected operations and production systems that learn on their own, automatically adapting to demand dynamics.
A true smart factory will integrate data from system-wide assets and help manufacturers maintain their equipment, track the inventory, and digitize their operations via their digital twin. The outcome of this integrated architecture is:
- A more efficient and agile system
- Less production downtime
- Broader network
- Ability to predict and adjust to changes in the facility
The cumulative result of all these factors will also enable manufacturers to position their products more competitively.
Technologies and processes that bring automation to the smart factory
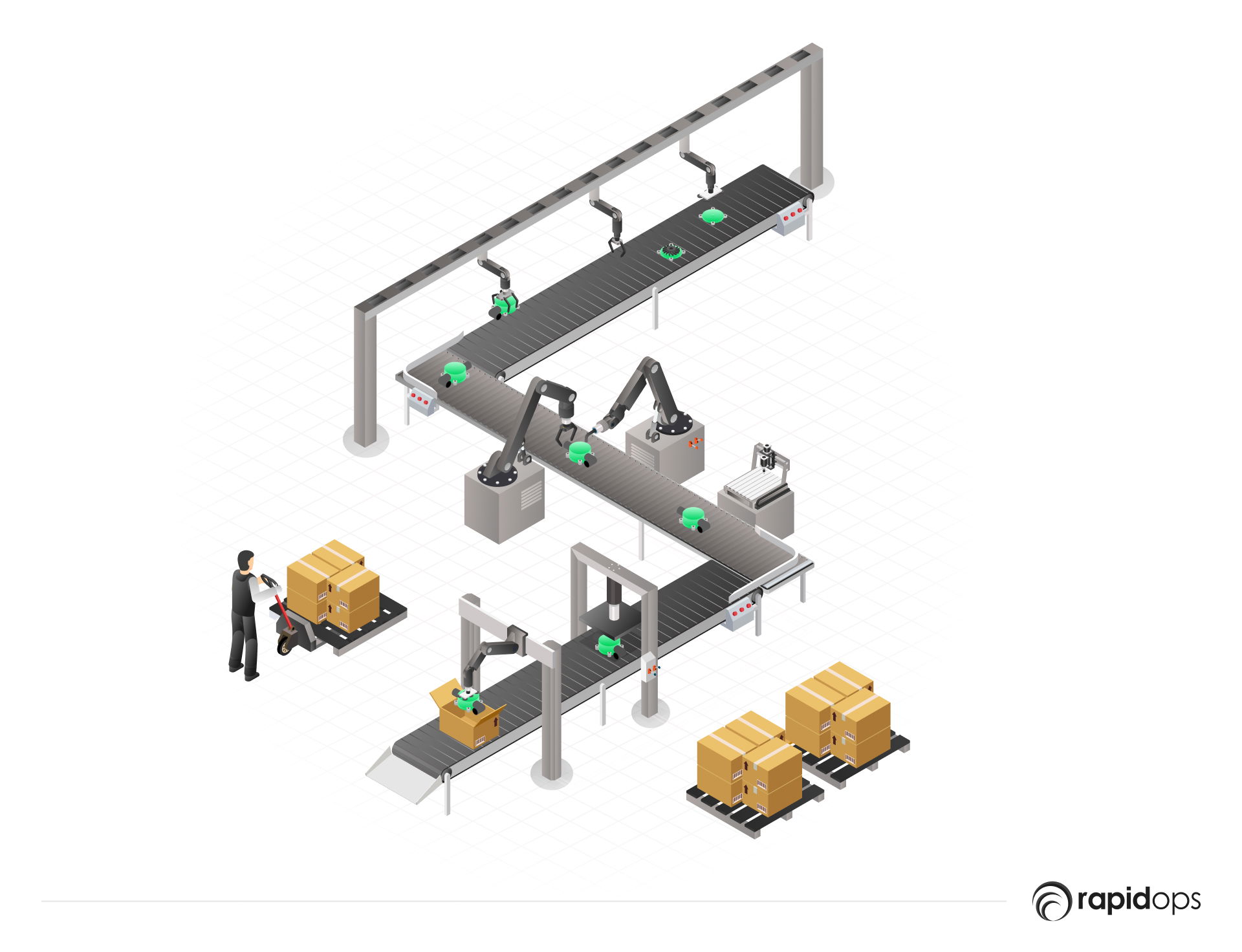
Modern manufacturers are embracing automation completely, or they are automating part of their processes. They might have tools necessary for automating various elements of their supply chain, such as:
- In-line production machinery
- Barcode scanners
- Drones for helping with pick-up and drop
They might also automate their entire production line using robotics to move products through various phases of the manufacturing process.
However, the majority of these individuals, yet automated processes, are disconnected from each other. This disconnected environment results in more human involvement where the workers are engaged in continuous analysis of disparate data sets and various reports for creating more efficiency.
In the future, smart factories will help manufacturers seamlessly optimize data and process workflows across their processes, from production lines to shops and sales offices.
What this recent pandemic showed businesses worldwide is that if the production assembly is halted for even one day, they are bound to incur millions in losses.
If we consider the smart factory revolution from an ergonomic, economic, and environmental point of view, it is sure to help manufacturers strive toward complete digital transformation.
Smart factories are the best option for manufacturers with the idea to capture and store the data of their entire product life cycle. Their basic goal is to create a manufacturing process that swiftly responds to the rapid changes in demand without incurring high costs.
Also, with the help of smart manufacturing, enterprises can access stored information whenever and wherever it is needed.
Let's talk about technologies here.
Internet of Things
By 2024, the number of IoT devices is expected to reach over 17 billion, which is twice the number of people on Earth, which shows how integrated technology is becoming. - Statista
Flexible IoT-enabled infrastructure connects machines and technologies with sensors and other information technologies. The global IoT market was valued at USD 330.3 billion and is expected to grow at a Compound Annual Growth Rate (CAGR) of 16.7% during the forecast period (2021-2026). The predicted revenue figure for 2026 stands at USD 650.5 billion.
Artificial Intelligence
AI is the simulation of human intelligence processes by machines, especially computer systems. These processes include machine learning (the acquisition of information and rules for using the information), reasoning (using rules to reach approximate or definite conclusions), and self-correction. It uses algorithms to analyze data.
Robotics and automation
Gone are the days when manufacturers invested in manually operated machines. Now, self-operating machines and robots are being used to minimize human intervention and improve efficiency and lead times.
Digital twins
A digital twin is a virtual representation of a product. It can be used in product design, simulation, monitoring, optimization, and servicing and is an important concept in the industrial Internet of Things. A digital twin is a model that is retained for later stages of the product's lifecycle, such as inspection and maintenance.
Sensors connected to the physical product can collect data and send it back to the digital twin, and their interaction can help optimize the product's performance.
Wearable and mobile technology
Smart glasses, gloves, smartwatches, and other tracking items can be worn on the body comfortably and are used to track and manage operations in real-time, as well as provide virtual reality assistance.
These technologies connect the systems, integrate the data, and ensure that operations are performed smoothly.
Connection of smart factory with ERP
A smart factory is an interconnected and highly advanced manufacturing process and production facility that makes data management, product management, and operations management streamlined and hassle-free. When ERP is implemented in a smart factory, we call it Intelligent ERP.
iERP (intelligent ERP) ties together innovative technologies to automate large-scale processes and expedite manufacturing execution time. It is a system of integration that uses all evolving technologies to track end-to-end operations.
The common smart factory challenges
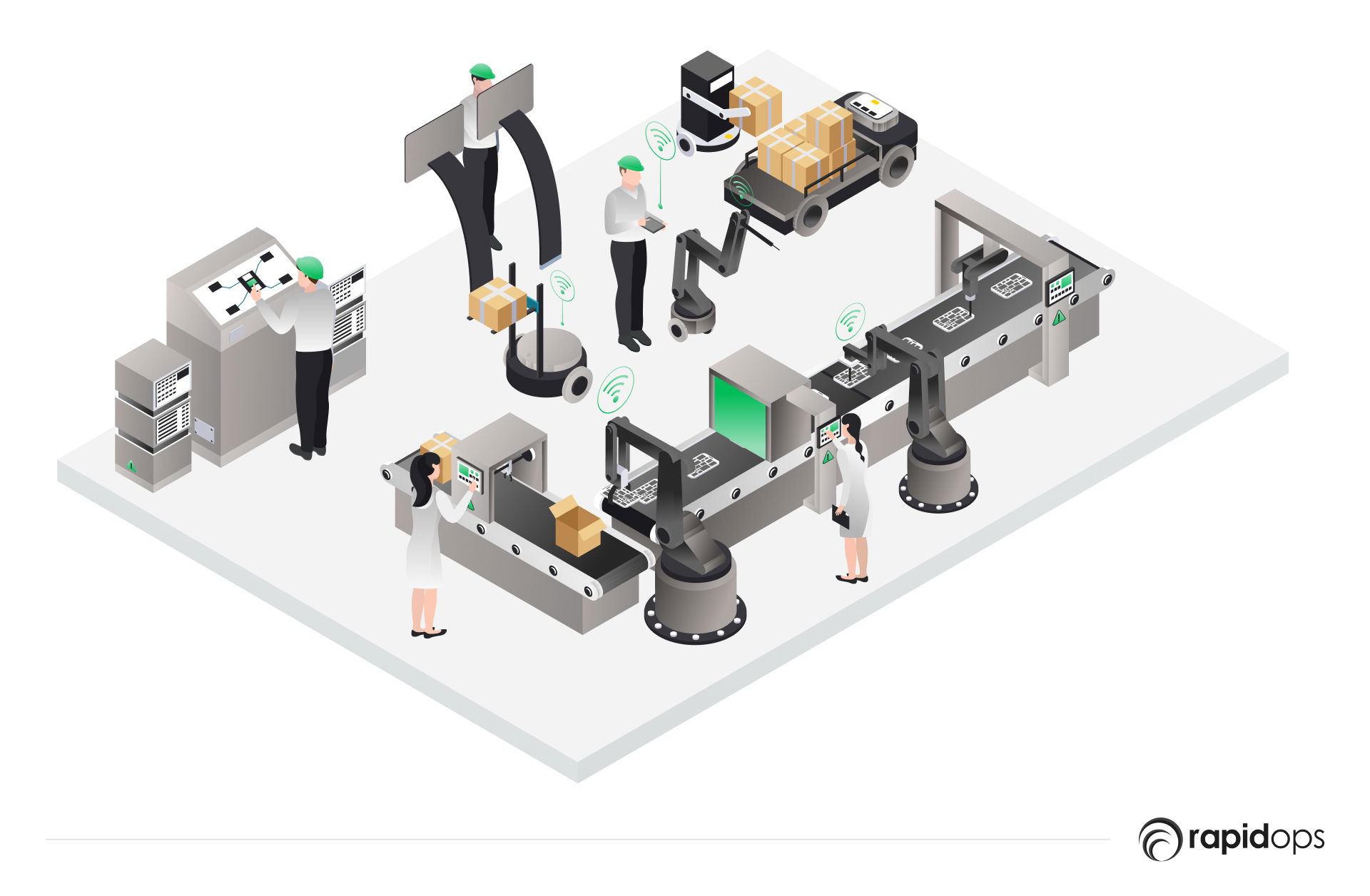
Now, let's take a look at the most common challenges that manufacturers face while implementing smart factories.
To make smart manufacturing successful, you need to look for a professional with expertise in programmable logic. It would be best if you were sure that the products implemented in the factory assembly line work and are compliant within a controlled factory floor.
Having off-the-shelf components
Be it the way the information flows and gets stored in the systems or is utilized in back-office virtualization.
For a successful implementation of your smart factory infrastructure, you need to look for vendors that can create full-custom designs that meet your industry's demands.
The quality and longevity of the connected devices you are going to include in this smart factory infrastructure play the most crucial role.
Complex supply chain
A complex supply chain with too much dependency on legacy systems means that your factory assembly line will have more human involvement.
Simplifying the supply chain enables manufacturers to allocate their resources to engineering better products and services. This allows the manufacturers to get to market quickly and gain faster ROI.
In order to create a simplified supply chain, manufacturers require a diverse set of solutions with multiple configurations that too with an expedited lead time. For manufacturers involved in global operation expansion, their supply chain must grow with the growing geographical reach.
The implementation of a smart factory will help companies gain detailed insight into their supply chain and be compliant with international regulations. They can also benefit from using unique codes to keep track of their production and distribution batches stored inside an easily accessible central data hub.
Compact lead times
To capture customers' attention and garner success in this competitive environment, manufacturers must quickly meet consumer expectations. To have lesser lead times, manufacturers must maximize supply chain efficiency.
Manufacturers require tailored inventory programs that will enable faster delivery in just a few weeks, outperforming average industry lead times.
Doing so enables manufacturers to reduce their development costs. Implementing this method also allows manufacturers to plan their roadmaps for product end-of-life visibility and avoid unnecessary disruptions.
Long-term availability of said technology
As a business owner with decision-making authority over various resources, you want to make a beneficial investment that lasts. Technology's longevity enables manufacturers to keep up production for as long as possible, maximizing the value of their investment.
For this, you require the aid of a technologically sound digital product development partner who will easily guide you regarding the longevity of various technologies that you require to be profitable.
Implementation of the smart factory for modern manufacturers
To move out of your legacy systems and scale up using smart factories might seem difficult and risky.
However, there are various benefits if you have modeled the perfect roadmap before diving into moving toward the modernization or digital transformation of your legacy production process.
- Successful implementation of the smart factory allows manufacturers to:
- Derive better value at lower production cost
- Increase product quality
- Reduce the time to market
- Higher sales growth
- Greater market penetration
- Increased profitability
To experience success with smart factory implementation, manufacturers must design their smart factory implementation with these guiding principles:
- Cultivate digital people
- Introduce Agile processes
- Configure modular technologies for production optimization
Seamless integration and automation – The new frontier for smart manufacturing
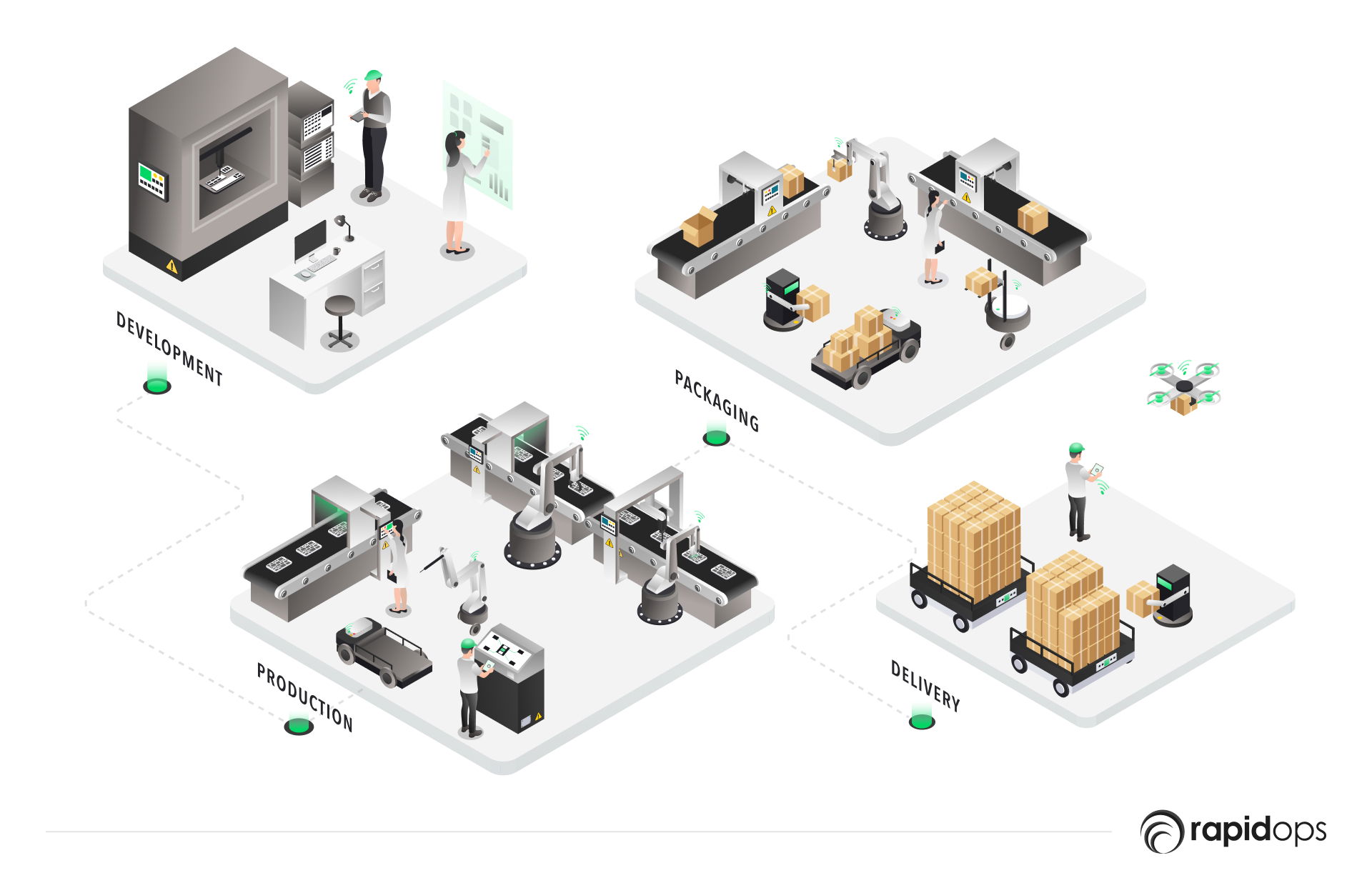
The revolution towards smart factories is creating a strong foundation for small and mid-sized manufacturers. By using technologies like IoT, cloud computing, big data analytics, machine learning, and artificial intelligence, the manufacturing sector is shaping its future for unprecedented success.
These technologies allow manufacturers to have a lean manufacturing structure and help them realize more profits from little investments.
They have a streamlined production assembly line that enables manufacturers to improve their product quality and reduce costs. Let's discuss the benefits manufacturers can derive from smart factories.
1. Optimized production
Establishing industrial IoT allows manufacturers to get their products off the production line at a faster rate. With the help of data analytics, they can process and understand all the data points spread across the product lifecycle and create a sleeker production cycle.
2. Smoother operation
Industrial IoT enables manufacturers to get real-time data directly from the production floor and respond rapidly to the changes in the system. Data allows them to tweak their operations at will, such as changing the operational schedule and machine settings.
3. Better ROI
With the faster transition to market due to higher productivity and greater efficiency, manufacturers can enjoy the due profits. Handling industrial data more efficiently helps manufacturers derive better opportunities. The smart factory promises faster reinvention and a better future for the manufacturers via:
- Deeper insights
- Slicker operations
- Digital technologies
4. World-class service
By employing industrial IoT, manufacturers not only gain better insights into their production cycle but also can create a feedback loop for the daily use of the manufactured goods.
With the help of smart factories, businesses can:
- Raise the level of their maintenance
- Offer wrap-around as-a-service packages
- Get feedback on their original designs for product improvement, customer satisfaction, and enhance brand loyalty
5. Room for innovation
When manufacturers use well-managed industrial data to increase efficiency in their production lines, they create opportunities for faster innovation.
They have the opportunity to reimagine and repurpose their products and services for the future based on the data they retrieve from product usage patterns and market demands.
6. Efficient asset management
Advancements in modern sensor technologies are enabling manufacturing industries to generate high-volume data. This data is continuously analyzed to reveal asset performance issues in a timely fashion.
The unique advantage that smart factories provide to manufacturers is that human intervention is eliminated when implementing a corrective course of action. In the future, businesses will take corrective measures by themselves using predictive analytics and machine learning.
7. Deriving lower cost of production
Smart manufacturing has allowed enterprises to operate with lower inventory, which lowers sourcing and supply costs. Material handling costs also drastically dip, decreasing downtime and wastage.
With low-frequency sensors now entering the production facilities, businesses consume less energy and can forget about quality compromise.
8. Improving the quality
As mentioned above, manufacturers can experience faster course correction with the help of smart factories with less human intervention. This same technology can also help them predict quality defects at a much earlier stage.
Such an intervention can greatly reduce scrapping rates and lead times, increasing the manufacturing unit's yield capacity.
We have witnessed the genesis of smart factories, and the journey is ongoing. Enterprises will need to consult digital partners that have expertise in creating an environment that can establish connected devices, low-frequency sensors, and other IIoT technologies.
Doing so will help move past the legacy infrastructure and move towards complete automation.
Conclusion: How can modern manufacturers scale up with the help of smart factories?
As per the data shared by the US Smart Manufacturing Leadership Coalition — a national alliance of manufacturing organizations, research universities, and government labs, there are some impressive estimates on the economic benefits of smart manufacturing:
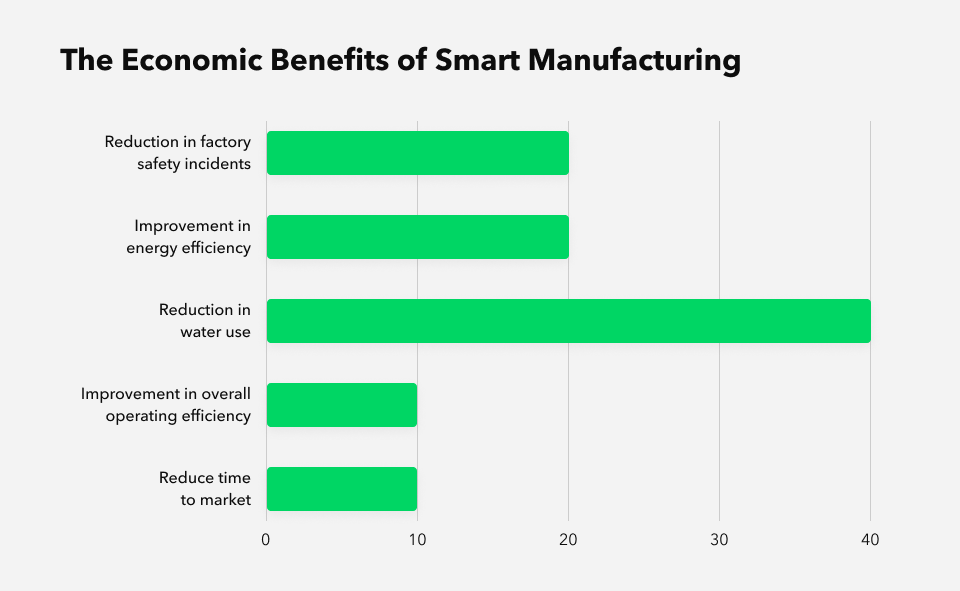
The above chart shows that smart manufacturing is still in its infancy. Business owners and decision-makers will require the help of experts who have successfully disrupted various sectors' legacy structures.
Rapidops worked for a client to create a complete automation system for their invoicing, purchase order, and discount approval. We created a modular and scalable solution that helped the client minimize the last-mile logistics delivery complexities with the help of intelligent automation and real-time GPS tracking.
With advanced algorithms, automated delivery notes, and real-time tracking, they reduced their operational costs. From the back office to the manufacturing plants, we allowed them to streamline their connected devices to cut costs and gain better ROIs.
If you want to discuss the roadmap for your smart factory infrastructure and move past the complexities of disparate systems, then do connect with us.
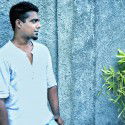
Saptarshi Das
Content Editor
9+ years of expertise in content marketing, SEO, and SERP research. Creates informative, engaging content to achieve marketing goals. Empathetic approach and deep understanding of target audience needs. Expert in SEO optimization for maximum visibility. Your ideal content marketing strategist.
What’s Inside
- Money, ease of use, and integrated system architecture
- A brief contribution of Factory 4.0
- Technologies and processes that bring automation to the smart factory
- The common smart factory challenges
- Implementation of the smart factory for modern manufacturers
- Seamless integration and automation – The new frontier for smart manufacturing
- Conclusion: How can modern manufacturers scale up with the help of smart factories?
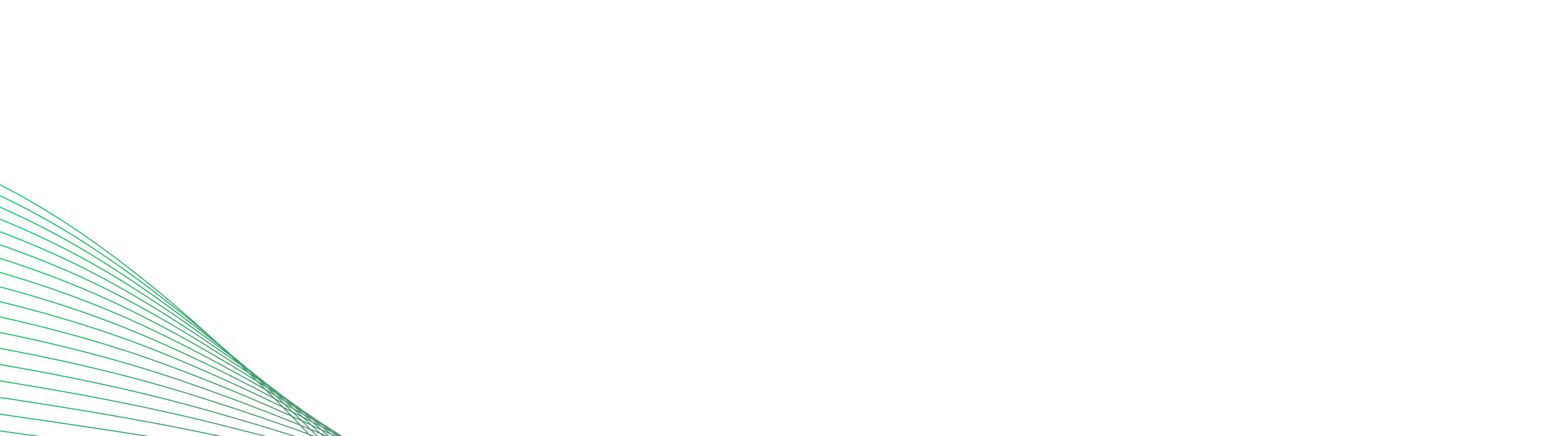
Let’s build the next big thing!
Share your ideas and vision with us to explore your digital opportunities
Similar Stories
- Strategy
- undefined Mins
- February 2017
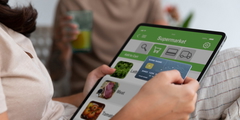
- Trends
- undefined Mins
- May 2021
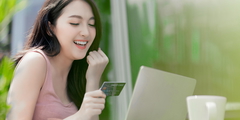
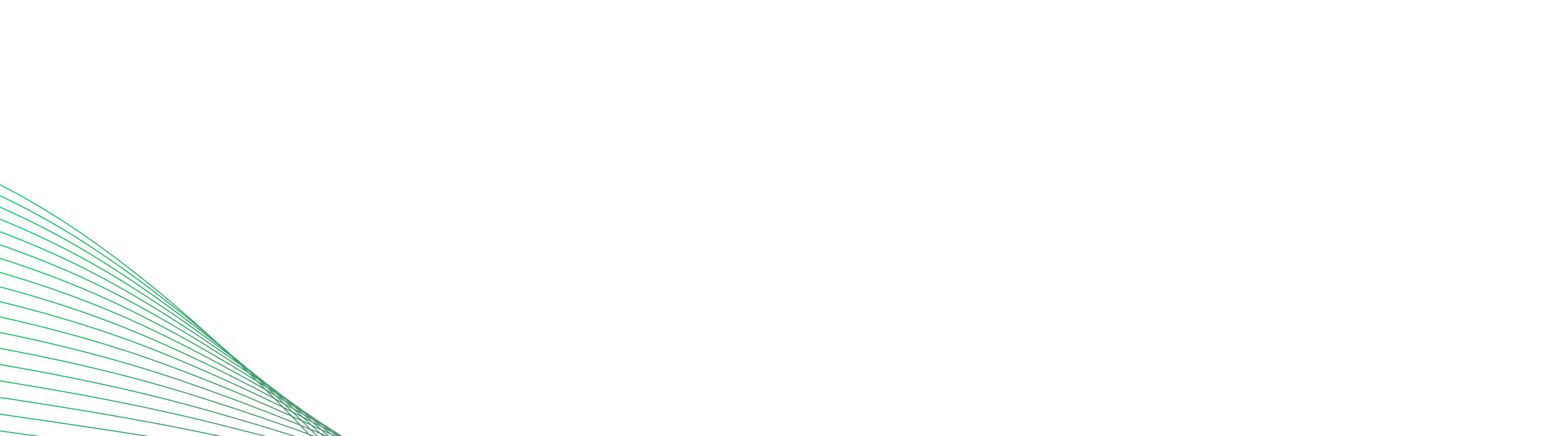
Receive articles like this in your mailbox
Sign up to get weekly insights & inspiration in your inbox.